Steam Temperature Control of Jacketed Tanks
Steam pressure control is vital for maintaining consistent tank jacket temperature
Tank temperature control is vital in many industries including chemical, polymer biopharmaceutical, and food and beverage to name a few. Processes using carefully controlled tank or kettle thermal environments oftentimes require precision control, fast response to temperature setpoint changes and even temperature distribution.
What is a jacketed tank?
A jacketed tank is used to control the temperature of the tank contents by circulating cooling or heating media in an enclosed “jacket” around the tank. Jacketed kettles or tanks are used to heat product rapidly and uniformly inside the kettle or tank to a certain setpoint for a process “recipe” and keep the product at the precise temperature setpoint for the duration of the process.
How is steam used in tank jacket temperature control?
Manufacturing facilities using steam utilities for their processes often generate steam in the boiler at high pressures to be used at various points in the manufacturing process. At the tank level, steam pressure is reduced in the line leading to the tank. Because the relationship between steam temperature and pressure is well understood, the steam pressure at the tank can be controlled to deliver a specified temperature to the tank.
Using pressure reducing valve to control steam jacketed tank
High pressure steam from the boiler can be reduced to the required jacket pressure by reducing the flow of steam with a globe valve at a set position or by using an orifice. However, any fluctuation in upstream flow rate will cause a fluctuation in pressure downstream. Using a pressure reducing valve (PRV) is a preferred method because it will open and close automatically to deliver precise downstream pressure to the tank despite any upstream pressure or flow fluctuations. See Fig. 1
Sliding Gate technology for steam pressure control
The Mark 60 PRV has proven to be an excellent choice for steam pressure control in jacketed tanks and kettles. The unique sliding gate design delivers unsurpassed accuracy, responsiveness and longevity with minimal maintenance required. The sliding gate has a short stroke and delivers steam in a straight through flow pattern for fast response to temperature setpoints or process fluctuations to keep tank temperatures at the exact recipe setpoint.
Whether preparing foods, sauces or drinks in food and beverage applications or combining ingredients in chemical and polymer processing, the Mark 60 will maintain accurate tank temperature using precision steam pressure control. Additionally, with its class IV shut-off steam will not be wasted between batches or when the process shuts down.
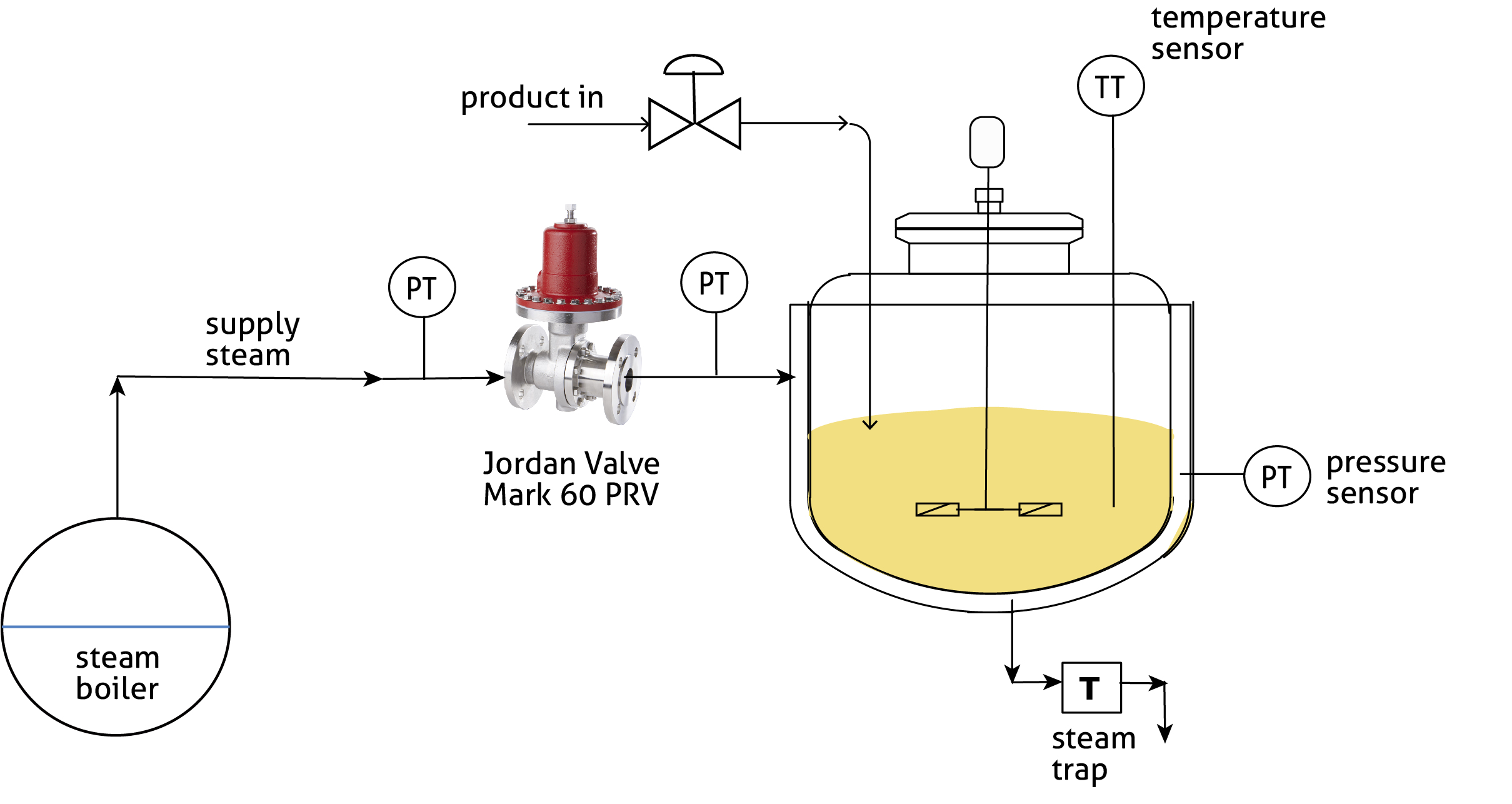
Fig. 1 A Jordan Valve Mark 60 PRV is reducing steam pressure from the boiler supply line to the tank jacket to control tank jacket temperature in a process tank
Application Spotlight: Chicken Soup processing in temperature controlled tank
As an alternative to using a Mark 60 PRV to control pressure between the steam supply and the tank jacket, a Jordan Valve Mark 80 self-operated temperature control valve could be considered.
At the customer facility in this spotlight, jacketed tanks are heated with steam to cook large quantities of chicken soup where good control and fast response are needed to adjust to load changes. They had been using a self-operated regulator prior to coming to Jordan Valve but they were not getting the desired temperature control performance.
After the customer installed a Jordan Mark 80 in their steam jacket line, they saw a noticeable improvement in temperature performance. The Mark 80 has the same sliding gate technology benefits as the Mark 60 but opens and closes the sliding gate based on an internal thermal sensor. It is completely self-operated and requires no external power source or expensive instrumentation to operate the valve. It offers the response time and tight temperature control the customer requires and is more commercially attractive than a control valve because it doesn’t need an external power source.
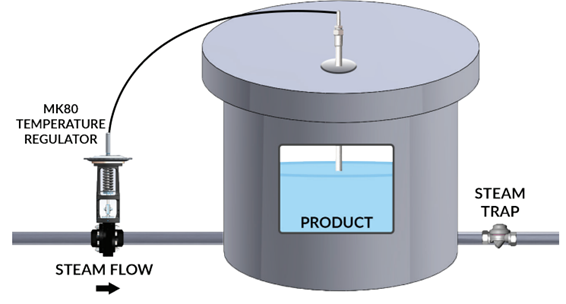
Let us help you find the right valve for your application.
Related Application Stories
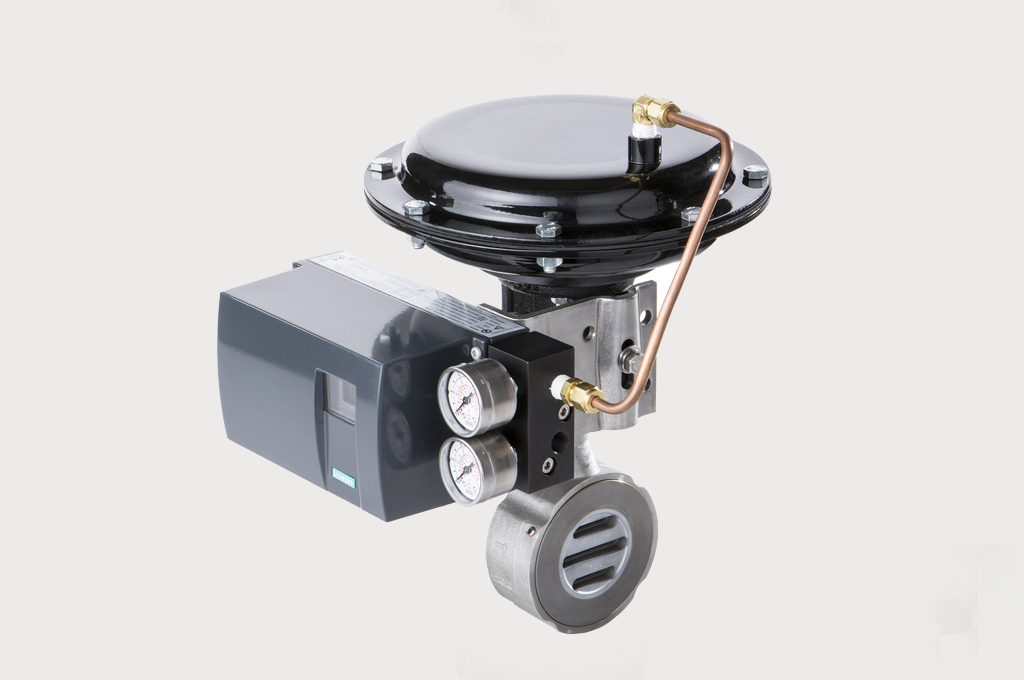
Steam Curing Cinder Blocks
Accurate steam control for precision autoclave dryer performance
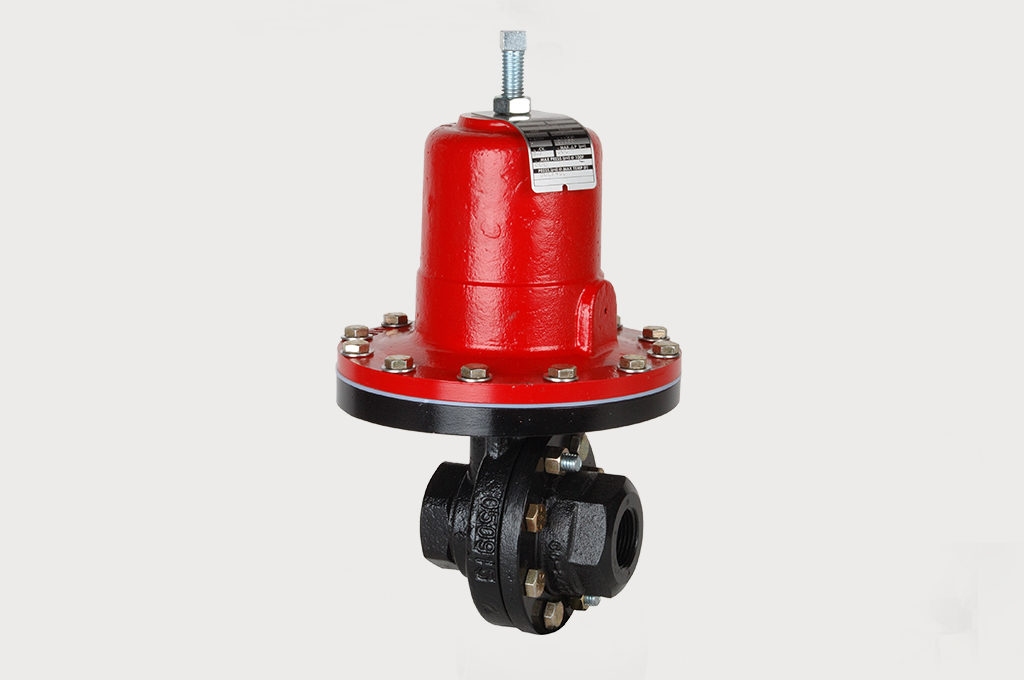
Steam Sterilization
Jordan Valve sliding gate valves with Jorlon® diaphragms outlast in challenging steam sterilizing process
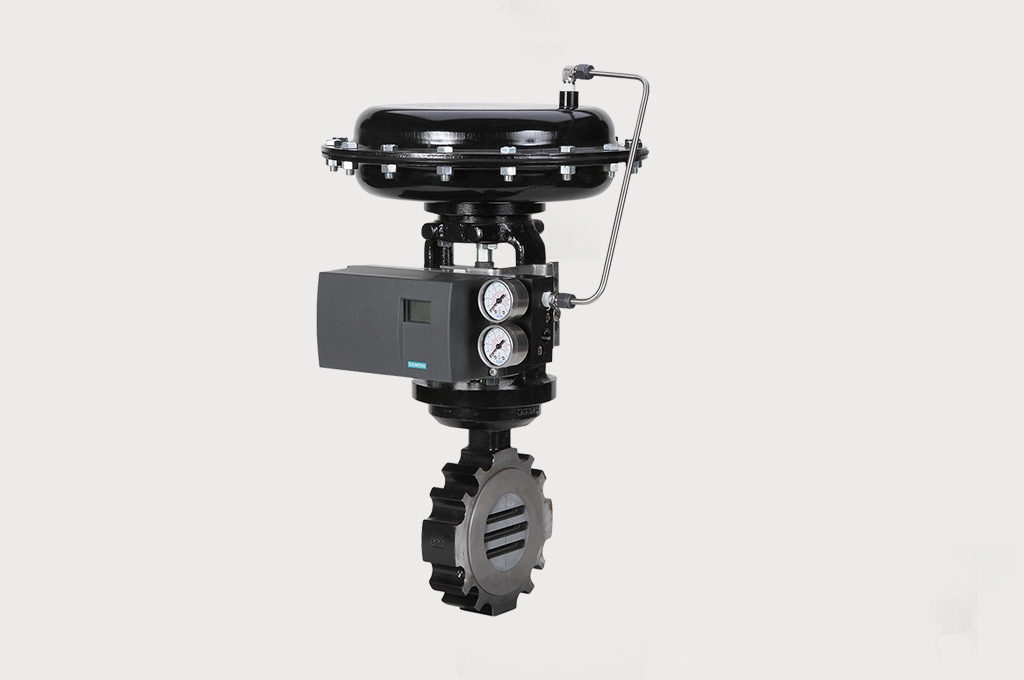
Precision Steam Control
Jordan Sliding Gate Valve for Precise, Efficient Steam Control
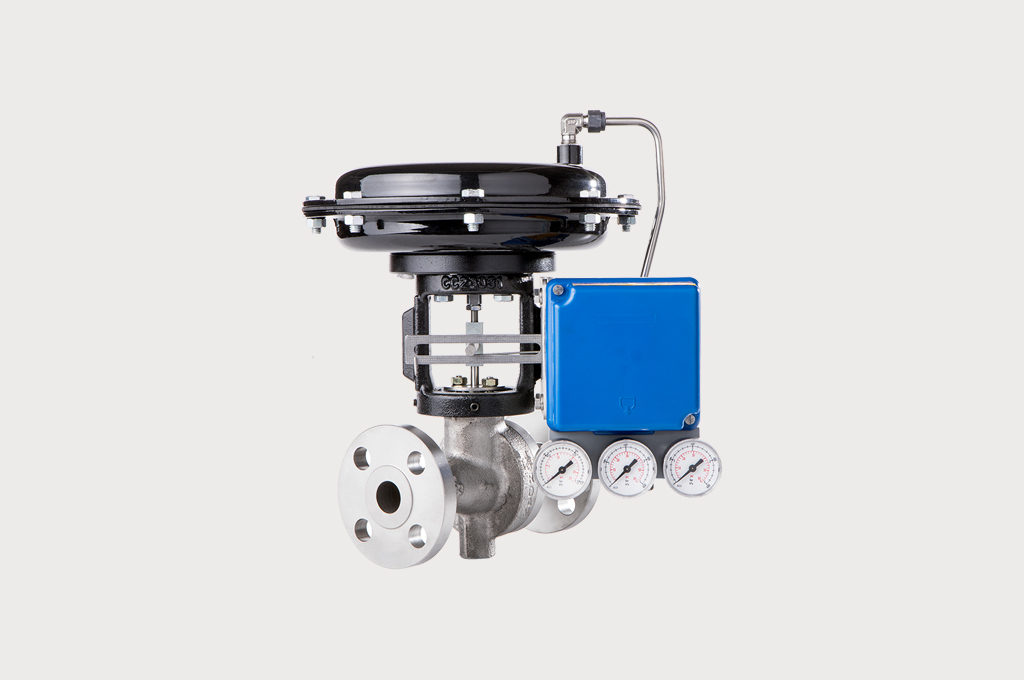
Steam Valve for Tire Curing Press
Jordan Valve sliding gate technology outperforms in challenging tire curing process
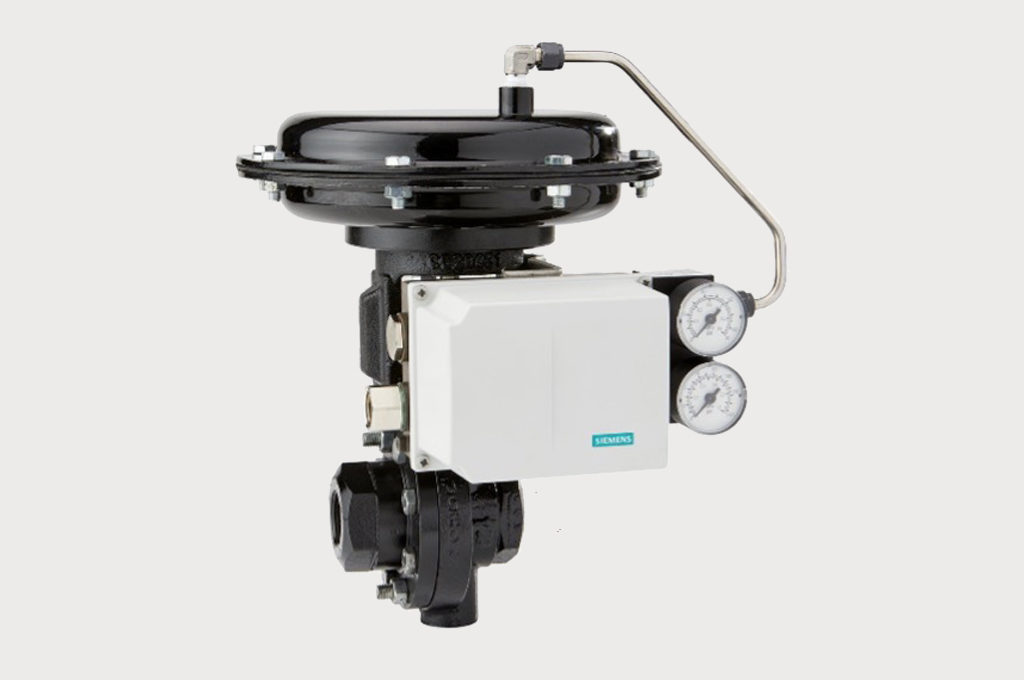
Better Steam Pressure Control Improves Drying for Coating Process
Jordan Mark 701 Sliding Gate Control Valves give Tighter Temperature Control, Faster Throughput
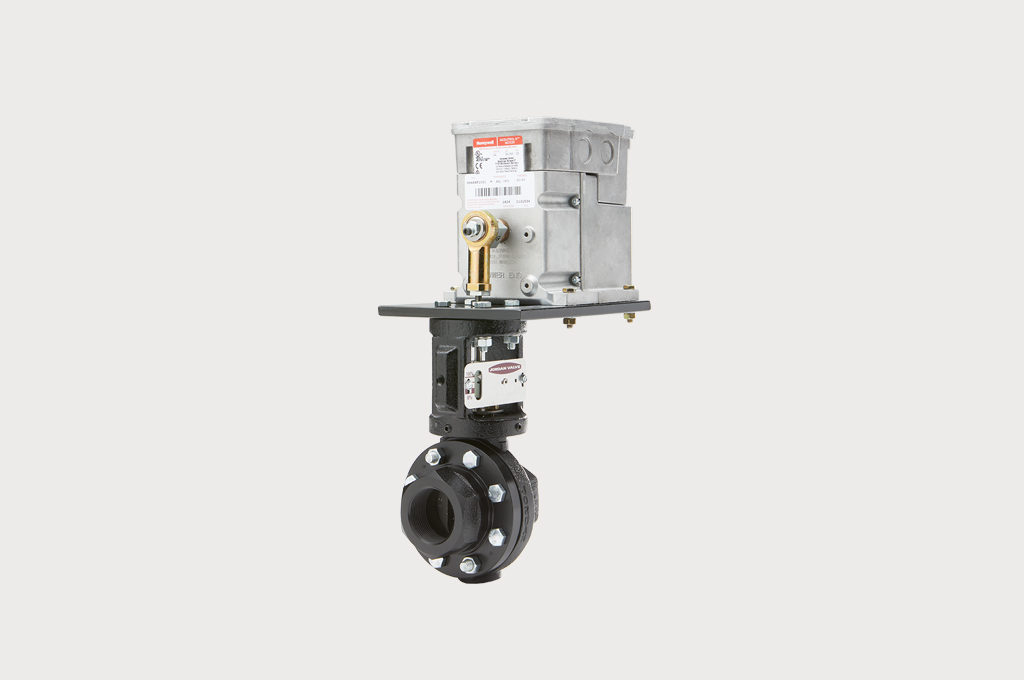
Boiler Feedwater Control
Jordan Mark 33 feedwater control valve maintains accurate level in boiler steam drum.
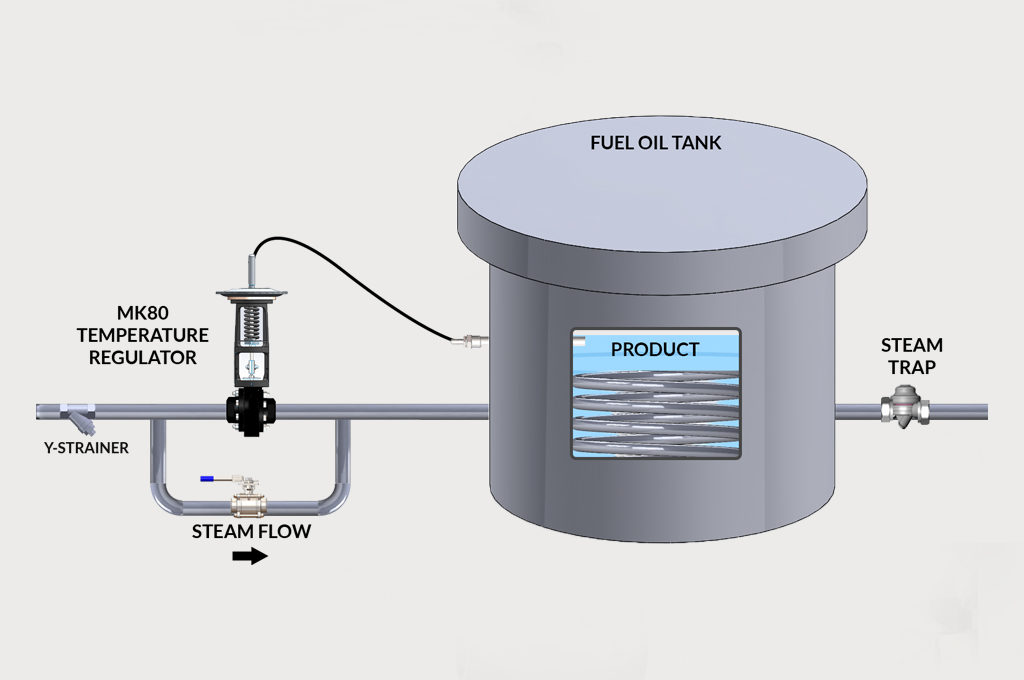
How Temperature Regulators and Control Valves Work
Using Self-Operated Temperature Regulators to Control Steam