How Temperature Regulators and Control Valves Work
Using Self-Operated Temperature Regulators to Control Steam
What is a temperature control valve or temperature regulator?
Temperature regulators and temperature control valves (sometimes referred to as TCV) are designed to control the temperature of a process by controlling thermal fluid pressure or flow in compressors, tank jackets, heating coils, or other heating elements. Temperature regulators are used in processes where temperature needs to be kept stable despite temperature changes in the surrounding environment.
What are the types of temperature regulators?
Temperature regulators can be self-actuated or externally actuated. Self-actuating temperature regulators are self-contained without the need for an external power source. They use thermally sensitive material that expands and contracts with temperature changes. The expanding and contracting results in movement of the actuator to adjust the valve position and change the flow path of the thermal fluid to the heating element. This mechanical actuation design results in excellent temperature control where the setpoint does not need frequent changes and is a more affordable way to effectively control temperature. Self-actuated temperature regulators are also called self-operated temperature regulators.
Externally actuated temperature control valves are often used as part of a more complex control system with an external temperature sensor and a Proportional-Integral-Derivative (PID) controller. They require an external power source for actuation. In a typical system, the PID controller is given a set point and gets feedback from the temperature sensor at the controlled point in the process. The PID controller compares the set point temperature to the process temperature from the sensor. An electronic or pneumatic signal is sent from the PID controller to the temperature control valve to adjust the valve position to keep the process at the temperature setpoint. This type of valve is used when frequent temperature set points are required for automation.
How do the Jordan Valve Mark 80 Series Temperature Regulators work?
The Jordan Valve Mark 80 Series is completely self-operated and requires no external power source or other expensive instrumentation to operate the valve. The actuator is connected to a sensing bulb by a capillary system that is filled with a volatile fluid that, when heated, begins to vaporize creating pressure in the system that works on the diaphragm to either open (reverse acting) or close (direct acting) the valve. A great deal of research has gone into the development of Mark 80 seal welded actuator (SWA) to provide the most precise control. Combined with the Jordan Valve sliding gate valve technology, the Mark 80 temperature regulator delivers excellent control. If the set point needs modifying, it is field adjustable, and the temperature range can be changed without taking the valve out of the line.
The Jordan Valve Temperature Regulator Series offers different configurations of self-operated temperature regulators for higher flows, fail open or close settings, tracing lines and pilot operation.
Application Highlight – Tank temperature regulation using steam heating coil
A company has a tank containing fuel oil that must be kept constant at 120°F for proper viscosity and flow properties. Steam is fed through coils inside the fuel oil tank to maintain the temperature setpoint. A Mark 80 Temperature Regulator controls the amount of steam through the heating coil.
The model used in this application contains Ethyl Chloride fill which provides temperature control between 80°F and 140°F (27°C to 60°C), to within 1°F of the set point. A series of Mark 80 models are available for temperature ranges from -40°F to 450°F.
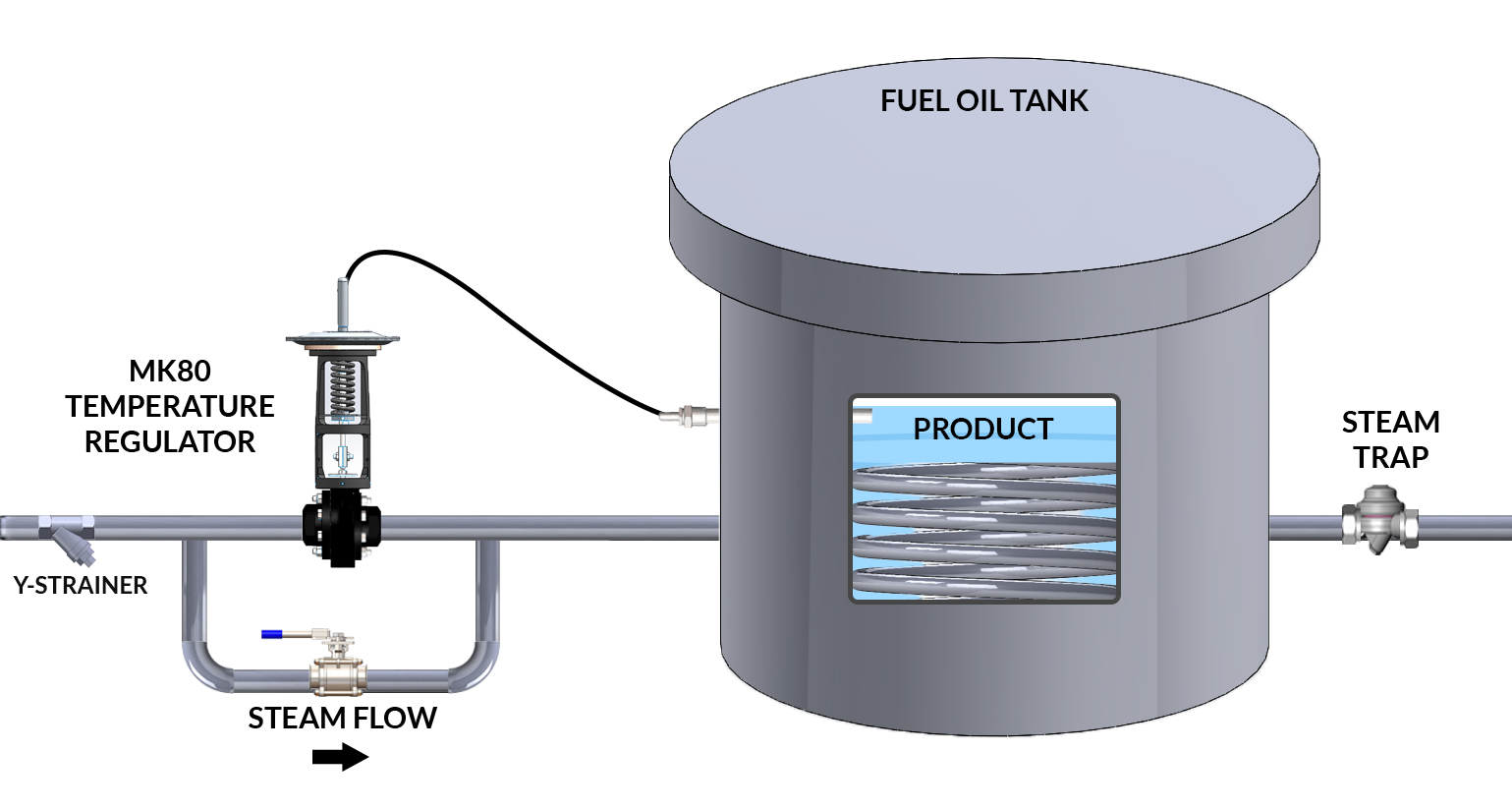
Application Spotlight: Air drying products
There are a variety of products that must be air dried prior to use such as lumber, tobacco, hops, tea and herbs. A simplified air drying process schematic is shown below. Steam-heated air is directed at the product drying rack. Behind the drying product is a finned sensing bulb connected to a Mark 80 temperature regulator. A finned bulb, designed for sensing air temperatures, increases the effective sensing surface area, providing the necessary sensitivity for air temperature control. It is used effectively in air ducts and drying kilns. When using a finned bulb, good air circulation is required, and the bulb is generally installed downstream of the blower fan.
The Mark 80 temperature regulator is actuated based on the bulb fluid pressure and increases or decreases steam flow into the coils, maintaining accurate air drying temperature.
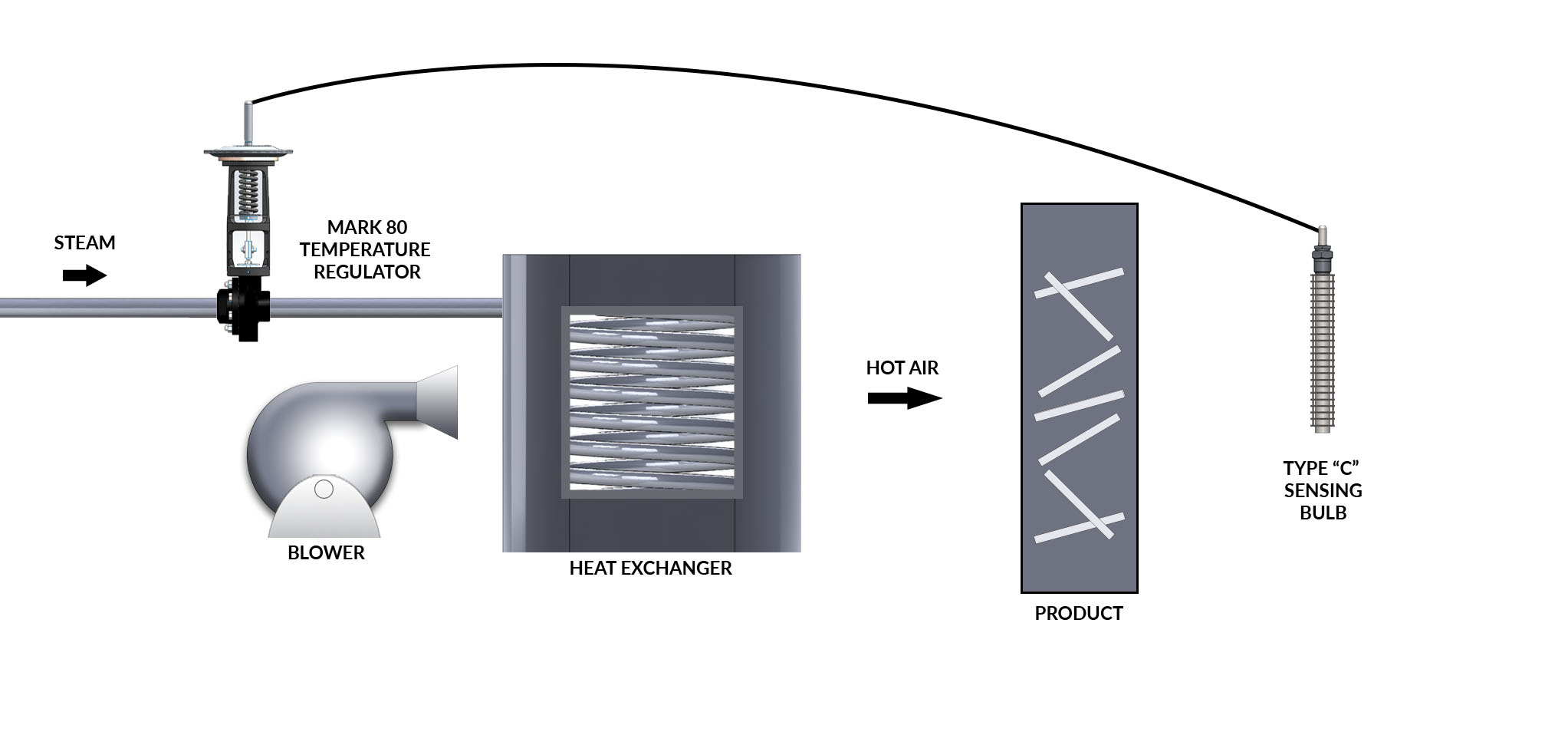
For information about how to use a self-operated temperature regulator in your process, contact us.
Let us help you find the right valve for your application.
Related Resources
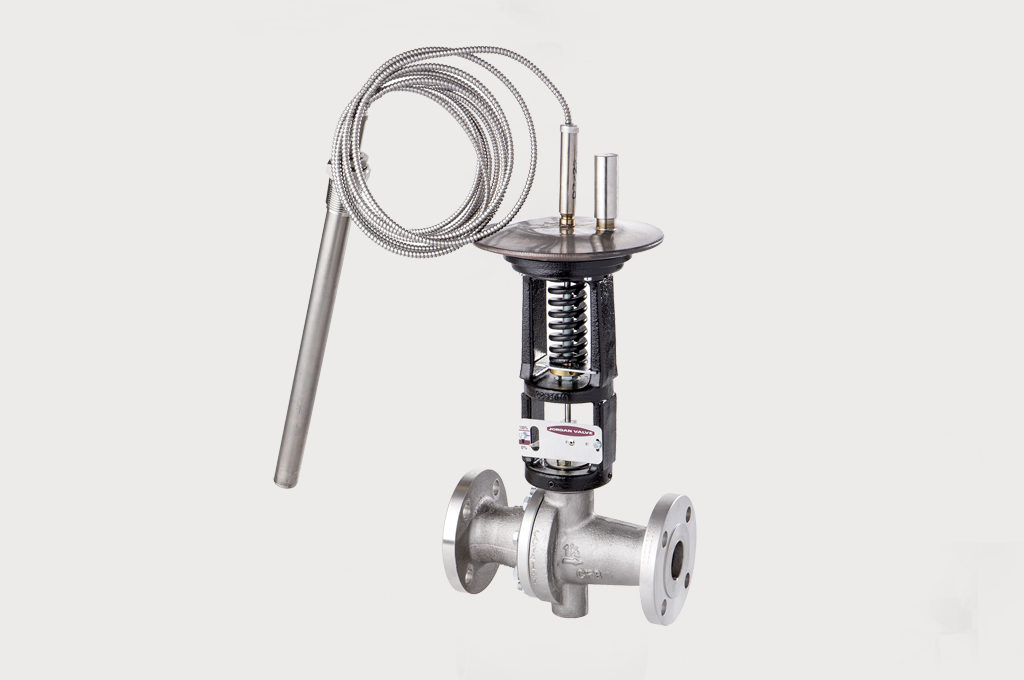
Steam Temperature Control of Jacketed Tanks
Steam pressure control is vital for maintaining consistent tank jacket temperature
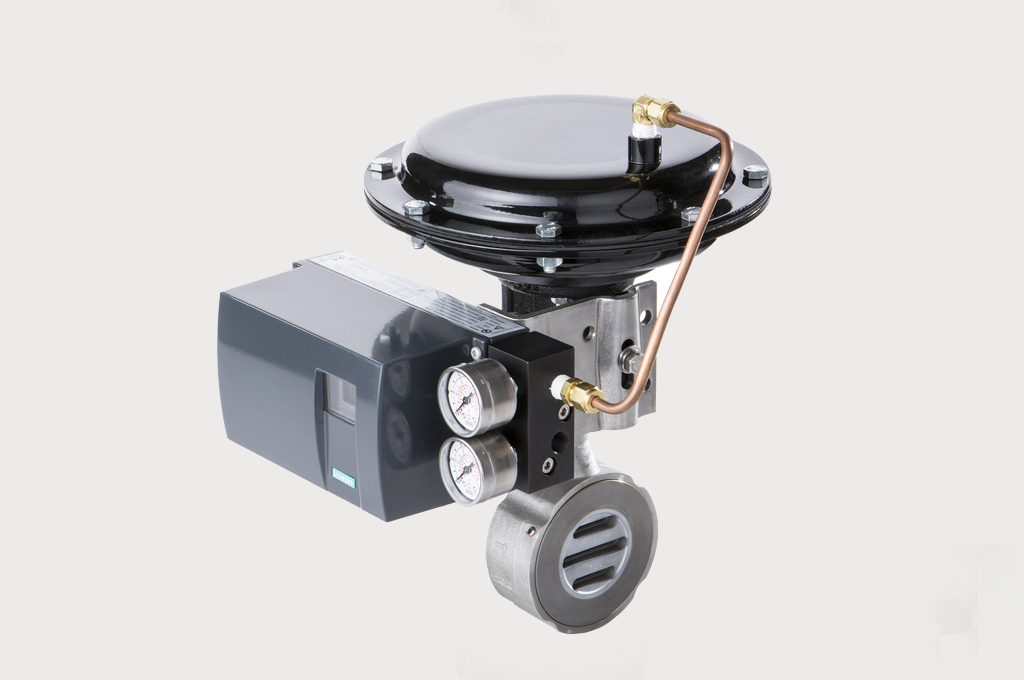
Steam Curing Cinder Blocks
Accurate steam control for precision autoclave dryer performance
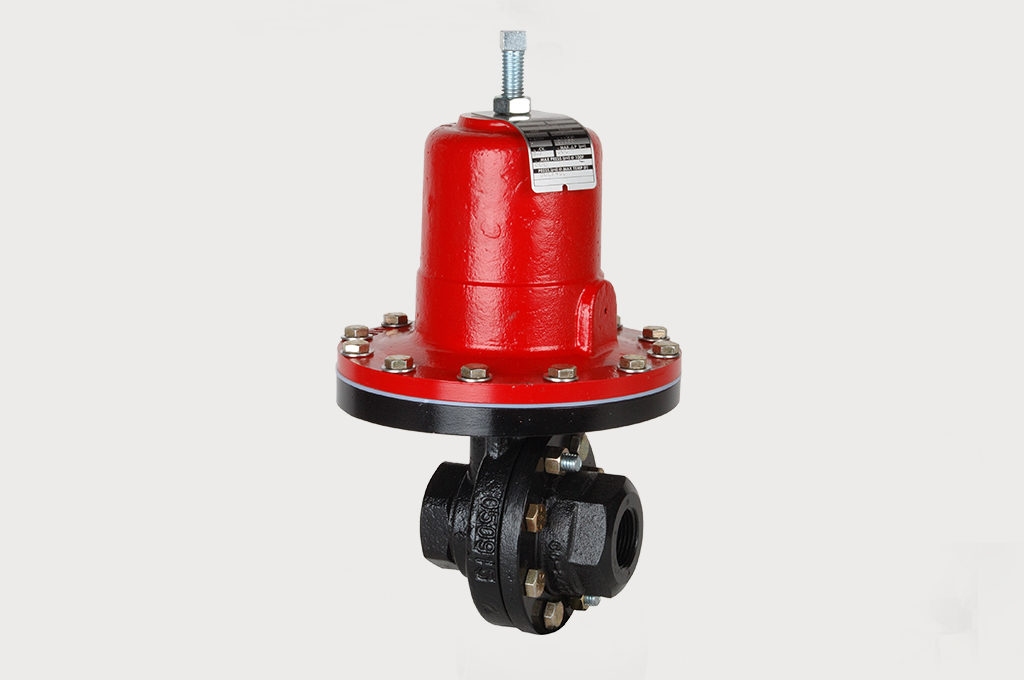
Steam Sterilization
Jordan Valve sliding gate valves with Jorlon® diaphragms outlast in challenging steam sterilizing process
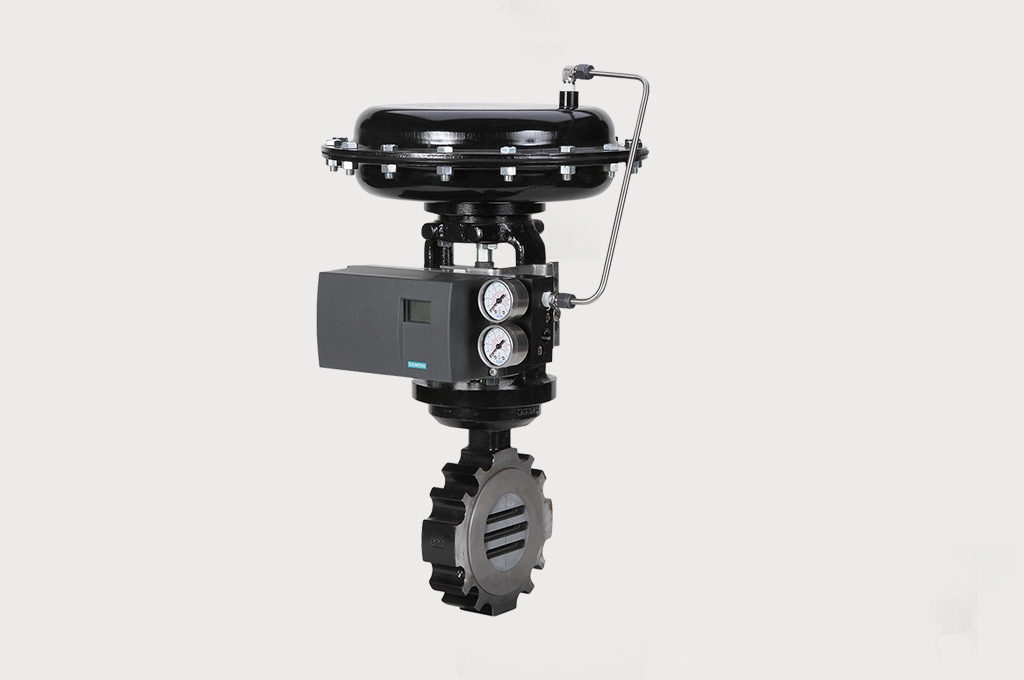
Precision Steam Control
Jordan Sliding Gate Valve for Precise, Efficient Steam Control
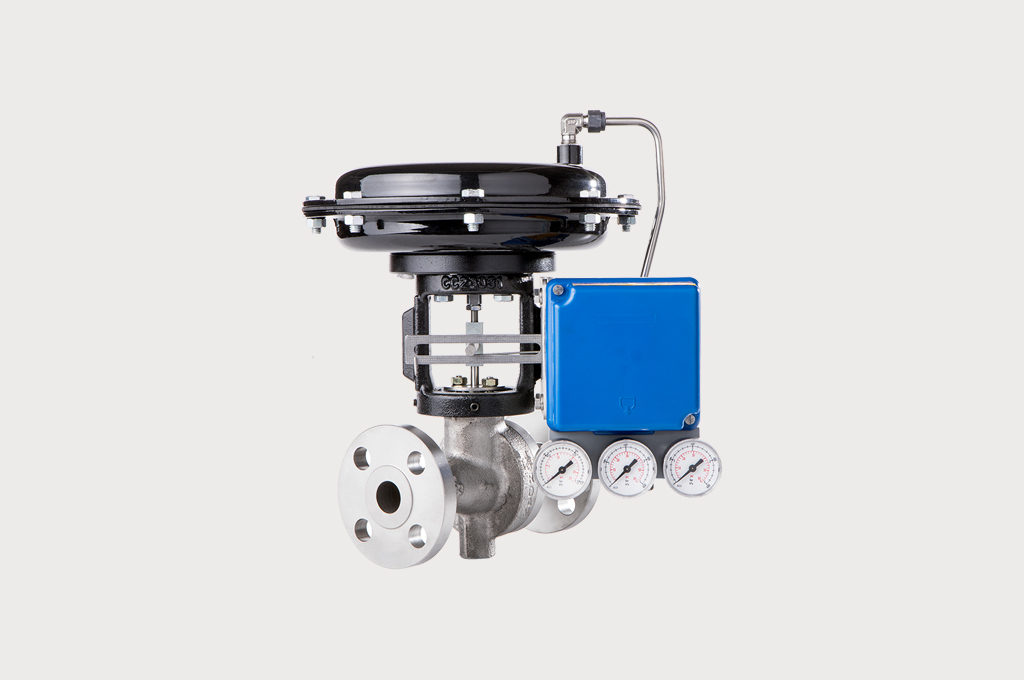
Steam Valve for Tire Curing Press
Jordan Valve sliding gate technology outperforms in challenging tire curing process
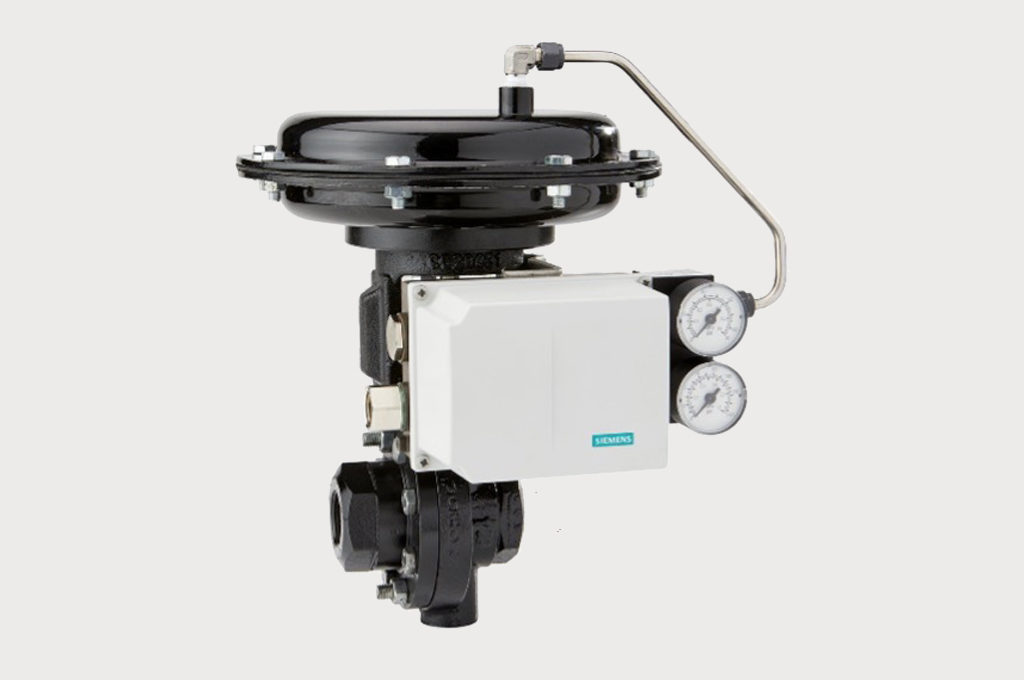
Better Steam Pressure Control Improves Drying for Coating Process
Jordan Mark 701 Sliding Gate Control Valves give Tighter Temperature Control, Faster Throughput
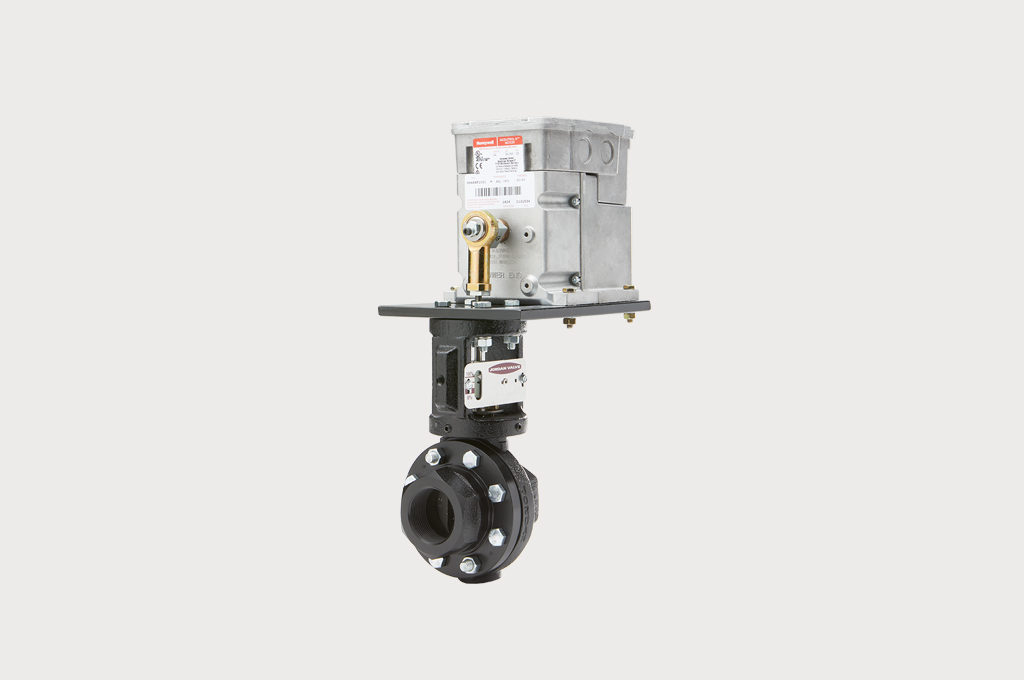
Boiler Feedwater Control
Jordan Mark 33 feedwater control valve maintains accurate level in boiler steam drum.